Understanding
Grease types and applications
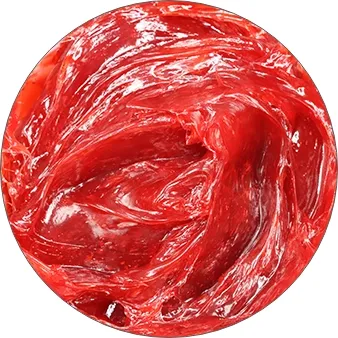
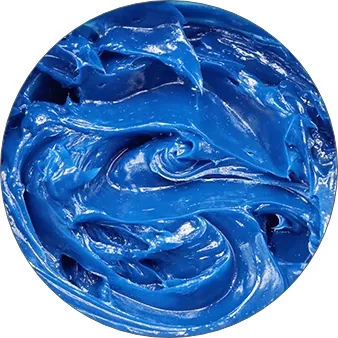
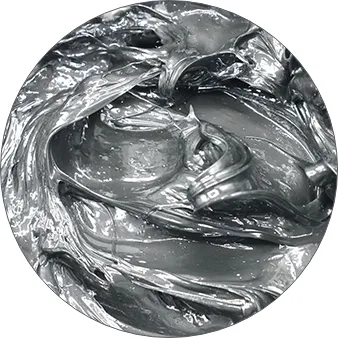
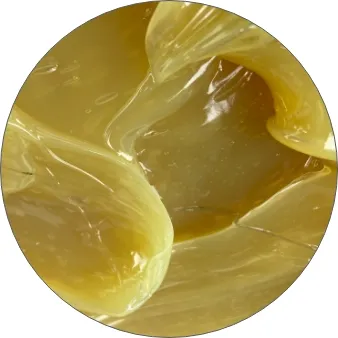
Selecting the right grease
How do you know if you’re using the right grease? You might be using a high-quality grease.
You may have put a lot of effort and money into selecting the best quality grease in the pursuit of lubrication excellence. But don’t confuse the quality of the lubricant with the quality of the specification.
Considering this lubricating oil analogy, the best quality turbine oil would most likely not make a good engine oil.
Most users are aware of the importance of selecting the right lubricant for a given application. When it comes to selecting lubricating oils for manufactured equipment, it’s easy to determine which products meet the original equipment manufacturer (OEM) requirements.
OEM specifications for a lubricating oil normally include viscosity at operating or ambient temperature, additive requirements, base oil type and even special considerations for different environmental conditions. Grease specifications, on the other hand, often lack the detail necessary to make a proper selection, leaving it up to the lubrication engineer to create the specification.
A common OEM grease specification might be to use an NLGI (National Lubrication Grease Institute) No. 2 lithium grease of good quality. Using this information alone, one could select the right consistency and thickener type. A similar specification for an oil-lubricated application would be to use a “good quality lubricating oil.” What?!
Due to the lack of specificity in most grease recommendations, it is important to learn how to properly select greases for each application in the plant.
Proper grease specification requires all of the components of oil selection and more. Other special considerations for grease selection include thickener type and concentration, consistency, dropping point and operating temperature range, worked stability, oxidation stability, wear resistance, etc.
Understanding the need and the methods for appropriate grease selection will go a long way toward improving lubrication programs and the reliability of lubricated machinery. Let’s walk through the grease selection process step by step, starting with the most important property.
Base Oil Viscosity
The most important property of any lubricant is viscosity. A common mistake when selecting a grease is to confuse the grease consistency with the base oil viscosity. Because the majority of grease-lubricated applications are element bearings, one should consider viscosity selection for those applications.
While most would not use an EP 220 gear oil for an oil-lubricated electric motor bearing, many people will use a grease containing that same oil for an identical grease-lubricated bearing. There are several common methods for determining minimum and optimum viscosity requirements for element bearings, most of which use speed factors, commonly denoted as DN or NDm.
Speed factors account for the surface speed of the bearing elements and are determined by the following formulas:
DN = (rpm) * (bearing bore) and
NDm = rpm * (( bearing bore + outside diameter) / 2)
The NDm value uses pitch diameter rather than bore diameter because not all bearings of a given bore have the same element diameter, and thus have different surface speeds. Knowing the speed factor value and likely operating temperature, the minimum viscosity requirement can be read directly from charts like Figure 1.
Figure 1 assumes the base oils’ viscosity index. To be more precise, one would need to use a chart that identifies the viscosity at operating temperature, then determine the viscosity grade from a viscosity/temperature chart for a given lubricant.
Additives and Base Oil Type
Once the appropriate viscosity has been determined, it’s time to consider additives. The additive and base oil types are other components of grease that should be selected in a fashion similar to that used for oil-lubricated applications. For instance, a lightly loaded high-speed element bearing does not require extreme pressure (EP) additives or tackifying agents, while a heavily loaded open gear set does.
Most performance-enhancing additives found in lubricating oils are also used in grease formulation and should be chosen according to the demands of the application. Figure 2 shows some common additive requirements by application. Most greases are formulated using API Group I and II mineral oil base stocks, which are appropriate for most applications.
However, there are applications that might benefit from the use of a synthetic base oil. Such applications include high or low operating temperatures, a wide ambient temperature range, or any application where extended relubrication intervals are desired.
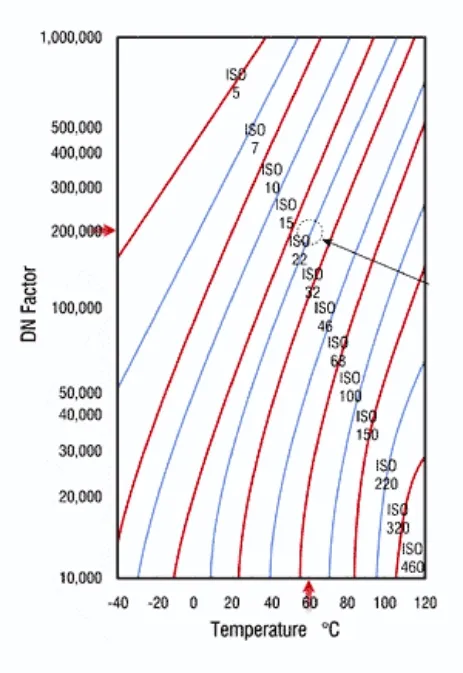
Figure 1. (Courtesy of ExxonMobil)
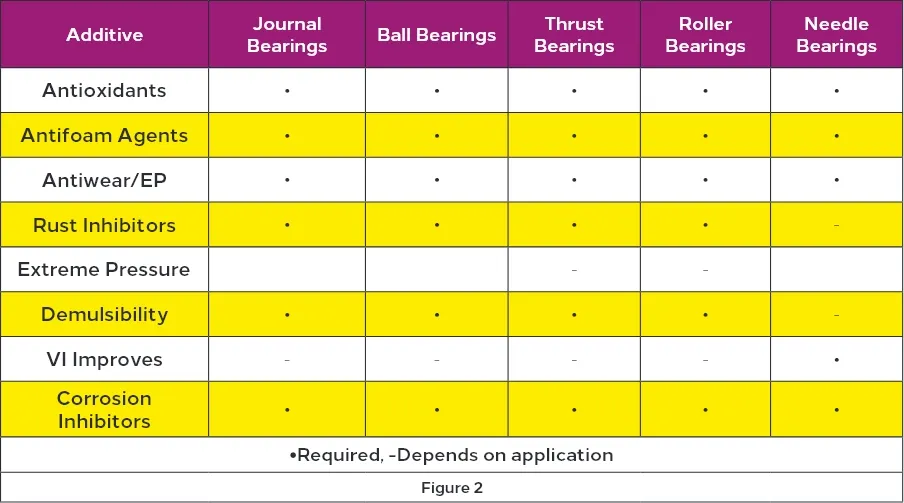
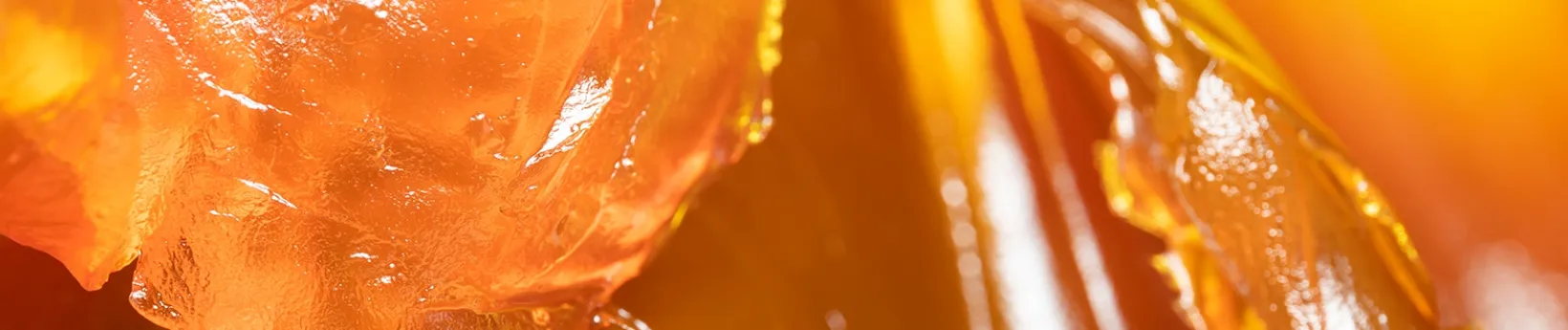
Grease Consistency and Thickener Type
Now for that extra step: The consistency of grease is controlled by the thickener concentration, thickener type and the viscosity of the base oil. Even though base oil viscosity affects consistency, it is important to note that a grease can have a high consistency and a low base oil viscosity or vice versa.
The NLGI has established a scale to indicate grease consistency which ranges from grades 000 (semifluid) to 6 (block grease). The most common NLGI grade is two and is recommended for most applications.
For bearings, speed factor and operating temperature can be used to determine the best consistency or NLGI grade for a given application. It may seem counterintuitive, but higher speed factors require higher consistency greases. Table 1 provides a general guide to selecting NLGI grade based on speed factor and operating temperature.
Numerous types of grease thickeners are currently in use, each with its own pros and cons. The most common types are simple lithium soaps, lithium complex and polyurea. Simple lithium soaps are often used in low-cost general-purpose greases and perform relatively well in most performance categories at moderate temperatures.
Complex greases such as lithium complex provide improved performance particularly at higher operating temperatures. A common upper operating temperature limit for a simple lithium grease might be 250°F, while that for a lithium complex grease might be 350°F. Another thickener type that is becoming more popular is polyurea.
Like lithium complex, polyurea has good high-temperature performance as well as high oxidation stability and bleed resistance. Thickener type should be selected based on performance requirements as well as compatibility when considering changing product types.
Performance Properties
Once the appropriate base oil viscosity, additive requirements and consistency have been determined, the remaining criteria to consider are the performance properties.
This is where the grease quality factors in. Grease performance properties include many of the same properties used for lubricating oils, as well as others exclusive to grease. Properties exclusive to grease include dropping point, mechanical stability, water washout, bleed characteristics and pumpability.
The most important performance properties are determined by the application. If an application operates continuously at room temperature, properties like dropping and upper operating temperature limits are not as important.
If an application operates under heavy loads at low speeds, an EP grease must be selected. It is important to remember that greases, like oils, have a careful balance of properties. A product may excel in one category and perform poorly in another.
For this reason, it is important to weigh each property’s significance relative to the intended applications to select the best overall fit.
Sometimes while trying to consolidate lubricants, it is easy to overconsolidate. Over time, this can lead to inaccurate lube specifications. A generic oil spec, including performance properties, should be configured for each lubricated point in the plant.
Armed with this generic specification, it is easy to select the right product no matter what brand is preferred. It is also important to review these specifications on a periodic basis to guard against specification creep.
While improving a lubrication program can be a tough job, lubricant specification is relatively easy. Armed with a little bit of knowledge and a few widely available tools, it is possible to rest easier knowing that the right grease is being used.
Grease thickener properties
Grease thickener compatibility chart
Consistency of grease
Lubricant Grease
NLGI Grade for Grease Consistency
Use this table to learn about the different NLGI consistency grades that lubricating greases can have.
Grease consistency depends on the type and amount of thickener used along with the viscosity of its base oil. A grease’s consistency is its ability to resist deformation by an applied force. The measure of consistency is called penetration, which is contingent on whether the consistency has been altered by handling or working.
ASTM D217 and D1403 methods are used to determine the penetration of unworked and worked greases. To measure penetration, a cone of a specific weight is allowed to sink into a grease for five seconds at a standard temperature of 25 degrees C (77 degrees F). The depth, in tenths of a millimeter, to which the cone sinks into the grease is its penetration.
A penetration of 100 would represent a solid grease, while a penetration of 450 would be semifluid. The National Lubricating Grease Institute (NLGI) has established consistency numbers or grade numbers from 000 to 6 that correspond to specified ranges of penetration numbers.
Certain conditions will affect the consistency required for a grease. The table below can help you select the correct consistency for an application.
5 Categories of Penetration
Undisturbed – Grease that is in its original container.
Unworked – A sample that has received only minimal disturbance in being transferred from the sample can to the test cup.
Worked – A grease that has been subjected to 60 double strokes in a standard grease worker. NLGI classification is based on worked penetration.
Prolonged Worked – Grease that has been worked the specified number of strokes (more than 60), brought back to 77 degrees F and then subjected to an additional 60 double strokes in the grease worker.
Block – This is the penetration of a block grease, which is hard enough to hold its shape without a container.
Additives
Additives can play several roles in a lubricating grease. These primarily include enhancing the existing desirable properties, suppressing the existing undesirable properties and imparting new properties. The most common additives are oxidation and rust inhibitors, extreme pressure, anti-wear and friction-reducing agents.
In addition to these additives, boundary lubricants such as molybdenum disulfide (moly) or graphite may be suspended in grease to reduce friction and wear without adverse chemical reactions to the metal surfaces during heavy loading and slow speeds.
It’s important to note that speed and load help determine the proper viscosity required for an application.
Remember, viscosity is the most important property of a lubricant.
Whenever you are selecting grease, you must also take into consideration the application and match the required consistency to ensure that you provide the equipment with the best choice to improve equipment reliability.
Grease composition
It is important to consider the grease composition. For example a bearing operating at high temperature may require some anti-oxidation additives or synthetic base oil. A grease operating under a shock loading condition would require anti-wear extreme pressure additives.
Therefore, when selecting a grease for an application, the following points are to be considered. Bearing type and dimensions; application influences such as temperature, load, and environmental factors such as heat, dust, chemicals in contact and water.
All these put together in consideration for application, environment and composition along with DN factor can help determine the most suitable grease
We are serving:
- Industrial
- Agriculture
- Automotive
- Locomotive
- Marine
- Textile
- Metal Works